Rendering - Odor and Opportunity
A colleague once commented to me, “that new assignment that you have at the rendering plant, just go ahead and throw up before you get there, it will save some time.” This engineer did not fully understand what the colleague was talking about until he arrived at the rendering plant during the summer. A rendering plant is exceptionally fragrant, and not in a good way.
So, for anyone who does not know, rendering plants are typically found near animal slaughtering operations. All the animal by-products that will never be on your dinner table are sent to the rendering plant to be converted into protein to be used in animal feed or fertilizer. Several EDT engineers, the author included, have learned that the odor from a rending plant represents opportunity and challenges. Rendering plants utilize unique equipment such as screw conveyors, large continuous cookers, fat presses, fat tanks, centrifuges, boilers, and a laundry list of other equipment items that from time to time are damaged due to an unexpected event.
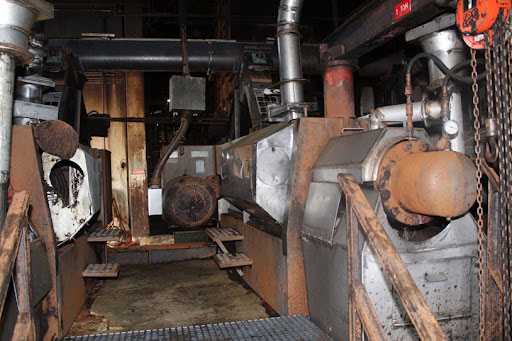
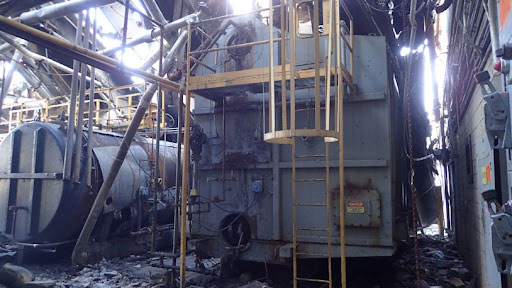
In the continuous rendering process, animal by-products are ground and then fed into a large steam-heated continuous cooking vessel. In the cooking vessel, the material is heated which evaporates moisture and frees the animal fat from the protein and bone. Upon exiting the cooking vessel, the material passes through a drainer screw conveyor which separates the liquid fats from the solids. The liquid fats are sent to a centrifuge to remove suspended solids and the remaining liquid is sent to finished fat storage.
The solid materials from the drainer screw conveyor, which are still very wet, go through a screw pressing operation that removes more liquid and most of the solid animal fat. The liquid and solid animal fat is recirculated back to the drainer screw conveyor settling tank where heavy bone and protein settle out of the remaining liquid. The solid materials from the screw pressing operation which is in the form of a press cake, is sent for further processing into protein and bone meal.
The rendering process produces significant amounts of water vapor mixed with non-condensable gases. This vapor stream is sent to a condenser which cools the vapor and removes the condensable gases. Non-condensable gases and other gases collected from the process are sent to an odor neutralization system.
EDT engineers have the knowledge and experience to evaluate the buildings, the utility systems, and the equipment damaged by these unexpected events for repairability vs. replacement, cost evaluation, time frame for repairs, and root cause analysis of the damaging event. The goal is to aid our clients in determining the cause of the event where possible and the most reasonable path to get facilities such as this rendering plant back in operation.
About the Author
D. Jeff Jaco III, M.E., P.E. is a District Engineering Manager and Consulting Engineer in our Columbia, SC Office. Mr. Jaco provides consultation in the areas of production process improvements and fire protection system evaluations including accidents in commercial, industrial, and residential settings; mechanical equipment damage assessment and repair and replacement cost estimates; and project estimating and scheduling. Furthermore, he performs engineering analysis and investigation of fire protection systems, boilers, plumbing and piping systems, HVAC systems, and gas systems. You may contact him for your forensic engineering needs at djjaco@edtengineers.com or (803) 791-8800.
Learn about how EDT Forensic Engineering & Consulting approaches scope of damage, and forensic engineering by assigning a file today.