Common Arc Welding Processes
Welding is a fabrication process whereby two or more parts are fused together by means of heat, pressure, or both, forming a joint as the parts cool. While it is possible to weld materials other than metal (plastics for example), the process is most often associated with the joining of metal parts. Arc welding is a form of welding where an electrical arc is used to generate the heat needed to raise the welded materials to their melting point and joined – in most cases with the addition of filler material having properties comparable to the materials being joined (steel fillers are used to join steel items, aluminum filler for aluminum, etc..). For the purpose of this discussion, we are going to focus on the arc welding of metals and the processes most often employed to construct the items we encounter on a daily basis.
The American Welding Society (AWS) has standard acronyms and definitions for many welding processes. However, these processes have more common field or industrial names, which we will also use in this discussion. Below are the welding processes we will examine:
American Welding Society (AWS) designation Common or Industrial name(s)
GMAW (Gas Metal Arc Welding) = MIG (Metal Inert Gas) welding
GTAW (Gas Tungsten Arc Welding) = TIG (Tungsten Inert Gas) welding
SMAW (Shielded Metal Arc Welding) = Arc welding or Stick welding
MIG welding process:
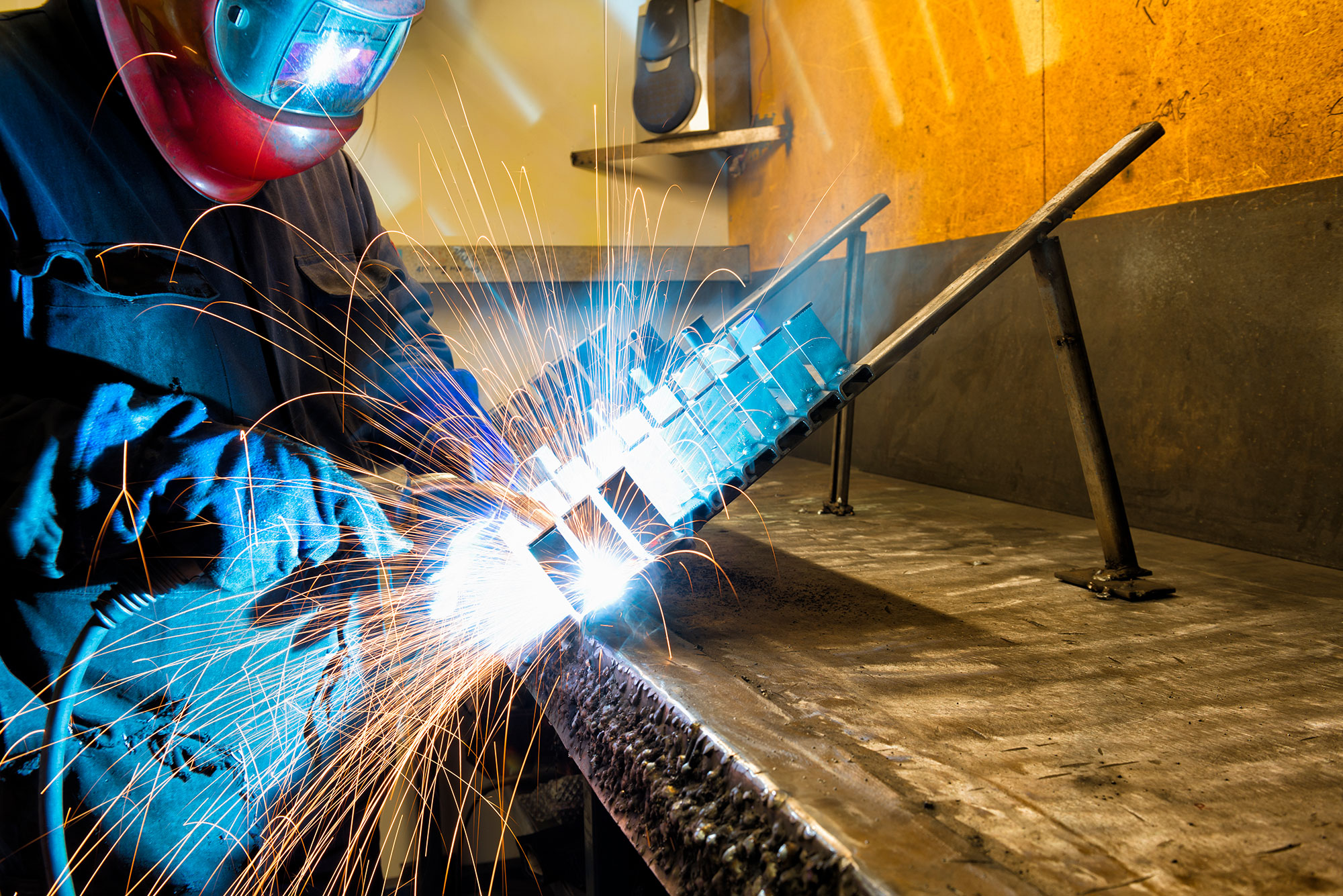
MIG (short for Metal Inert Gas) welding is among the most common welding processes utilized today, MIG is utilized in a variety of applications. Simply put, MIG welding is characterized by the feeding of an energized wire electrode into the “puddle” of molten metal forming the weld joint. The purity of this molten metal puddle/joint is maintained by surrounding it in an inert (non-reactive) “shielding” gas, most often Carbon Dioxide, Argon, or a mix of the two. The presence of this shielding gas prevents the molten metal puddle and filler from reacting with (and becoming contaminated by) oxygen, moisture, and other reactive airborne contaminants. The MIG process can be adapted for use with thin or thick metals by varying the voltage of the arc and the rate at which the wire is fed into the weld puddle. It is not difficult to find examples of MIG welded items in our daily lives. MIG is often used in automotive construction, for joining vehicle frame components, exhaust pipes, seat frames, torque convertors and other various components. MIG welds can also be found on playground equipment, handrails, bicycles, and other applications where sections of steel tubing are joined together.
MIG welded joint on steel:
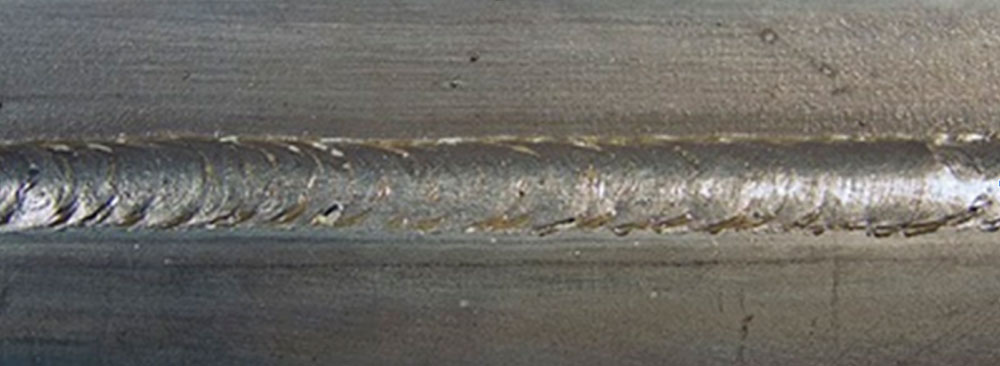
MIG Welding is also suitable for use on items constructed of aluminum such as aluminum boats, trailers, and other various applications. While MIG welding of steel often makes use of large spools of wire weighing 10-30 lbs., aluminum wire lacks the rigidity of steel wire. As such, aluminum wire cannot be pushed from the welding power source (where the spool is usually located) to the work area without buckling or binding before it reaches the welding torch. Because of this, welders of aluminum often make use of a spool gun, a welding torch/handpiece that houses small (typically 1lb) spools of wire in the handpiece rather than in the welding power source (aka – welder), requiring the wire to be pushed only a few inches rather than the usual several feet from the spool to the weld puddle. For high-volume, production applications where the use of smaller spools of aluminum is not practical, a “push-pull” system that utilizes a welding torch that contains a motorized feed mechanism that pulls the wire through the welding torch lead feeds the wire from the welder (the machine/power source, not the person) to the weld puddle. In general, MIG welding is favored for the high rates of productivity and ease of use it offers. As far as the limitations of MIG welding, the fact that it makes use of a shielding gas makes it vulnerable to weld contamination in windy environments where the shielding gas may be blown away from the weld puddle, leading to the formation of porous, contaminated welds that may not withstand the demands of their intended applications. Keeping this limitation of the process in mind, the MIG welding process is well suited for use in factory/production welding environments where climate conditions are more or less controlled.
Stick welding process
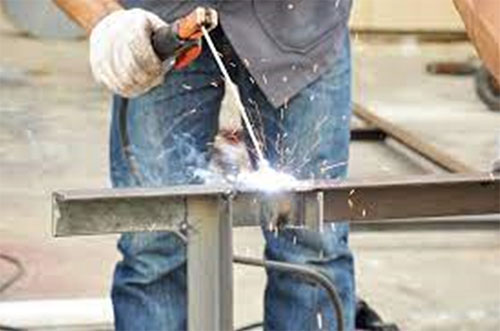
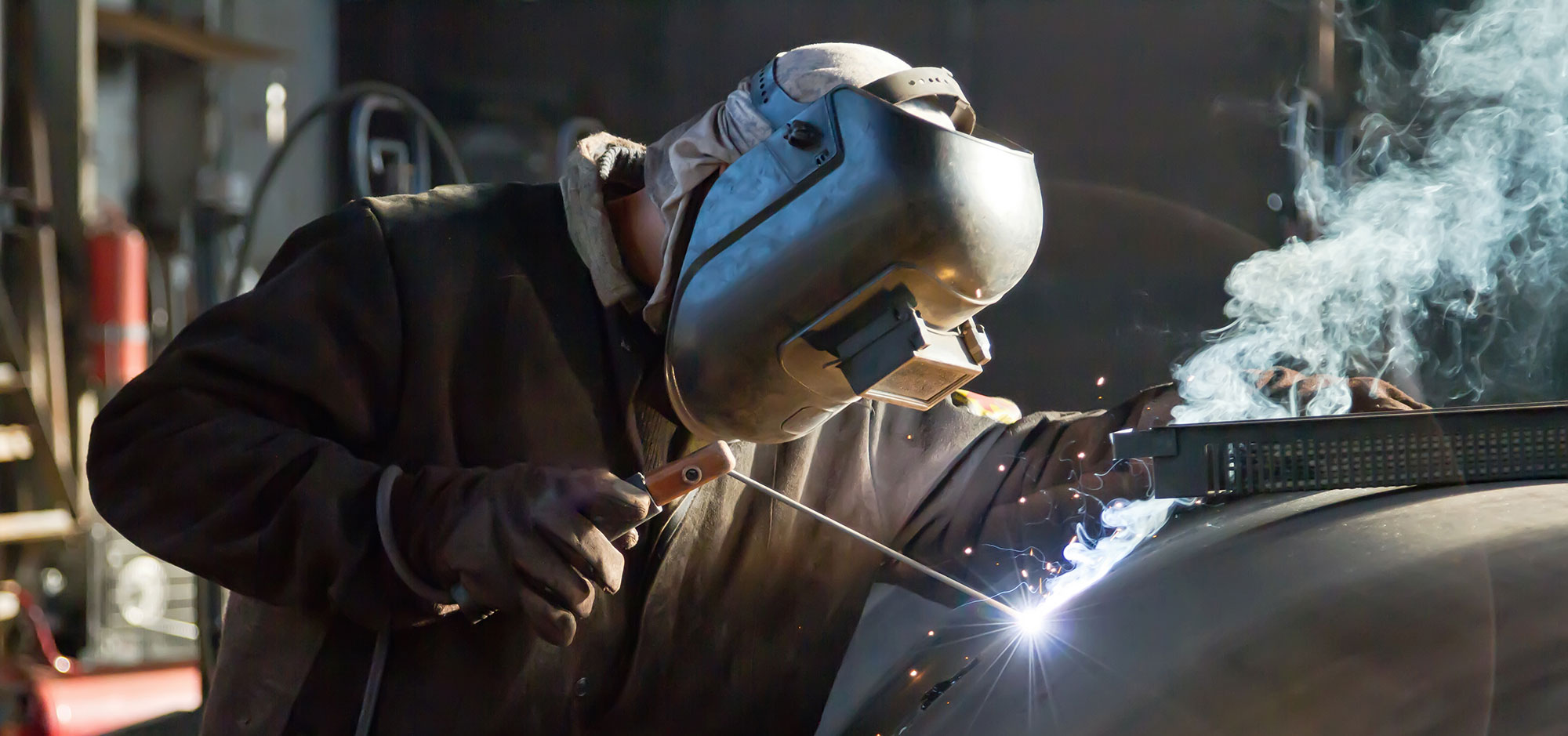
The oldest and most common arc welding process is “stick” welding, also referred to as SMAW (short for Shielded Metal Arc Welding). This process makes use of a flux-coated metal welding electrode – aka welding “stick” or rod. The flux coating on a welding rod serves the purpose of the shielding gas utilized in the MIG welding process, protecting the weld from contamination. Flux coatings can also affect the rate at which the weld puddle cools, thereby influencing the final strength of the weld. The composition of the flux coating can also influence the suitability of a welding rod for use in various positions (overhead, vertical, etc.). While it does serve a similar purpose in protecting/shielding the weld, flux does not dissipate like the MIG process shielding gas. Instead, flux often leaves a crust or “slag” over the weld that must be chipped away to reveal the weld.
Stick weld appearance, slag chipping
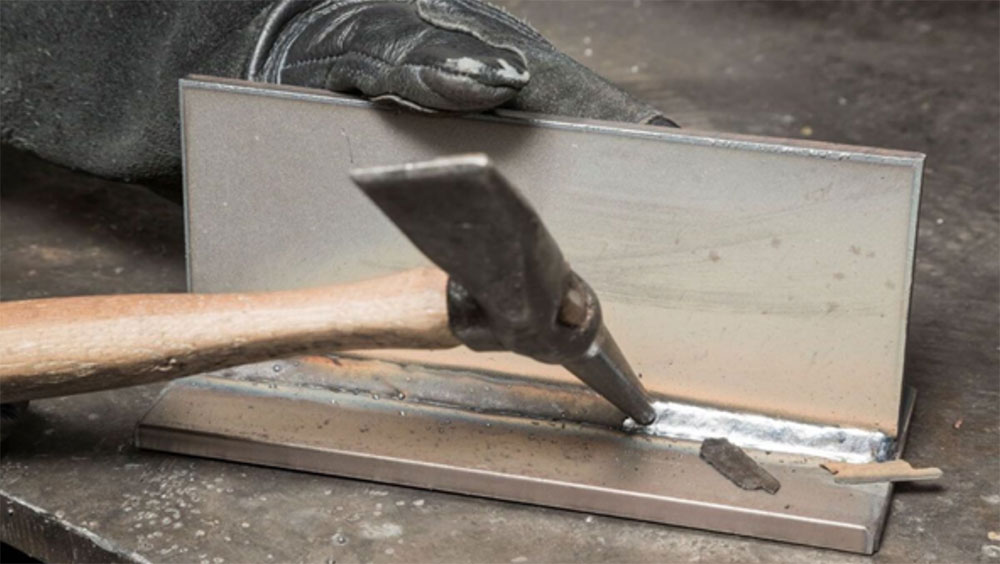
Stick welded joint, slag chipped off
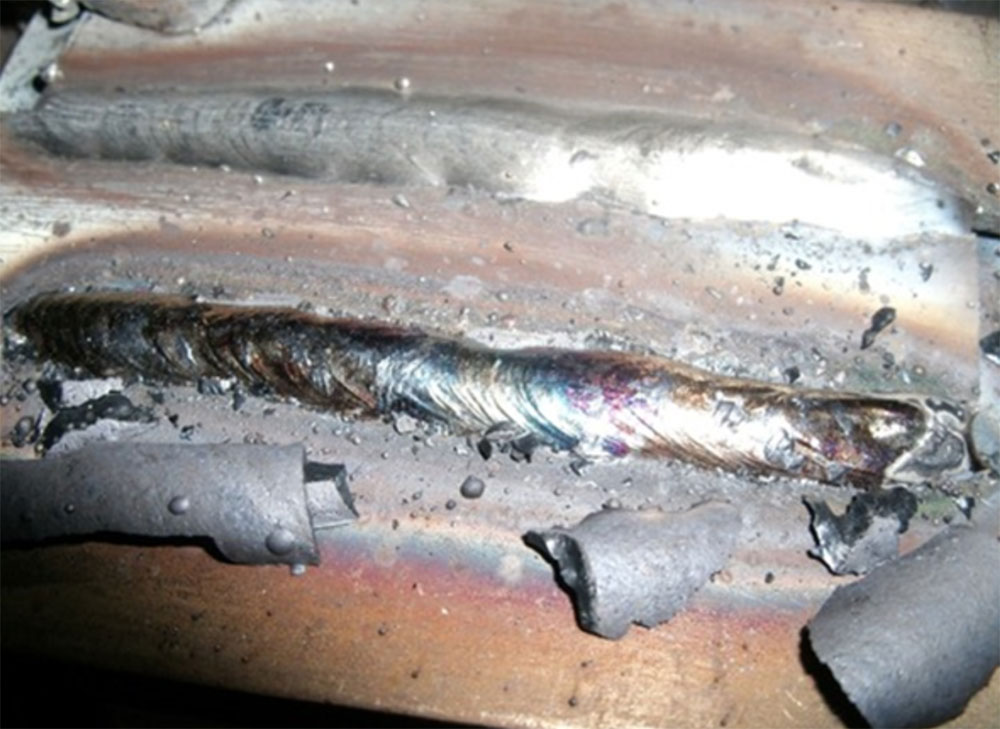
In addition to creating slag over the welds, this process also tends produce more smoke/fumes and spatter (splattered beads of material) than the MIG process, making it somewhat less desirable for indoor use – that said, the stability of the SMAW process makes it an excellent choice for outdoor welding such as the welding of structural steel, as well as field repairs of agricultural, construction, mining, and material handling equipment. Welding electrodes (or “rods” as they are commonly called) for the SMAW process are available in various compositions that make them suitable for specific tasks. For this process, after the electrical arc is established or “struck” (deemed so as the process resembles striking a match), the welding electrode is manually fed into the weld puddle by the weldor (the person, not the machine/power source). This contrasts with MIG welding where feed rate of the wire/electrode is pre-set before the weld is started, according to the needs of the joint being formed. Similar to MIG welding, where the wire/electrode diameter may be varied to suit the needs of a particular joint, stick welding makes use of electrodes of varying diameters for that purpose. Regarding the adjustment of the TIG/SMAW process for varying metal thicknesses, the electrical current is varied (increased for thicker metals/larger electrodes) rather than varying the voltage as with MIG welding. This being the case, power sources for MIG welding are not readily interchangeable with those used for stick welding applications. In general, the SMAW/Stick welding process is favored in windy/outdoor welding and other sites where it is not practical to move a MIG welding machine to the location where the welding is being completed. In addition to working well in windy environments, stick welding may also be completed underwater. Yet another desirable trait of stick welding is the simplicity of the equipment. Compared to a MIG welder which requires mechanisms to manage the feeding of wire and shielding gas as well as a power source to generate the arc, a stick welding machine requires only a power source. This being the case the initial cost of equipment tends to be lower. While MIG welding usually takes place within a few feet of the welder/power source, it is not uncommon for stick welding to be completed 50-100’ away from the power source. This is particularly helpful in structural steel applications where the weldor (person) must move between various and often elevated locations where it would be impractical to move MIG equipment from one location to the next. While it may not be the most favored for some applications, stick welding has been around a very long time and will likely remain the overall most common type of welding, considering the low cost and versatility of the process.
TIG welding process
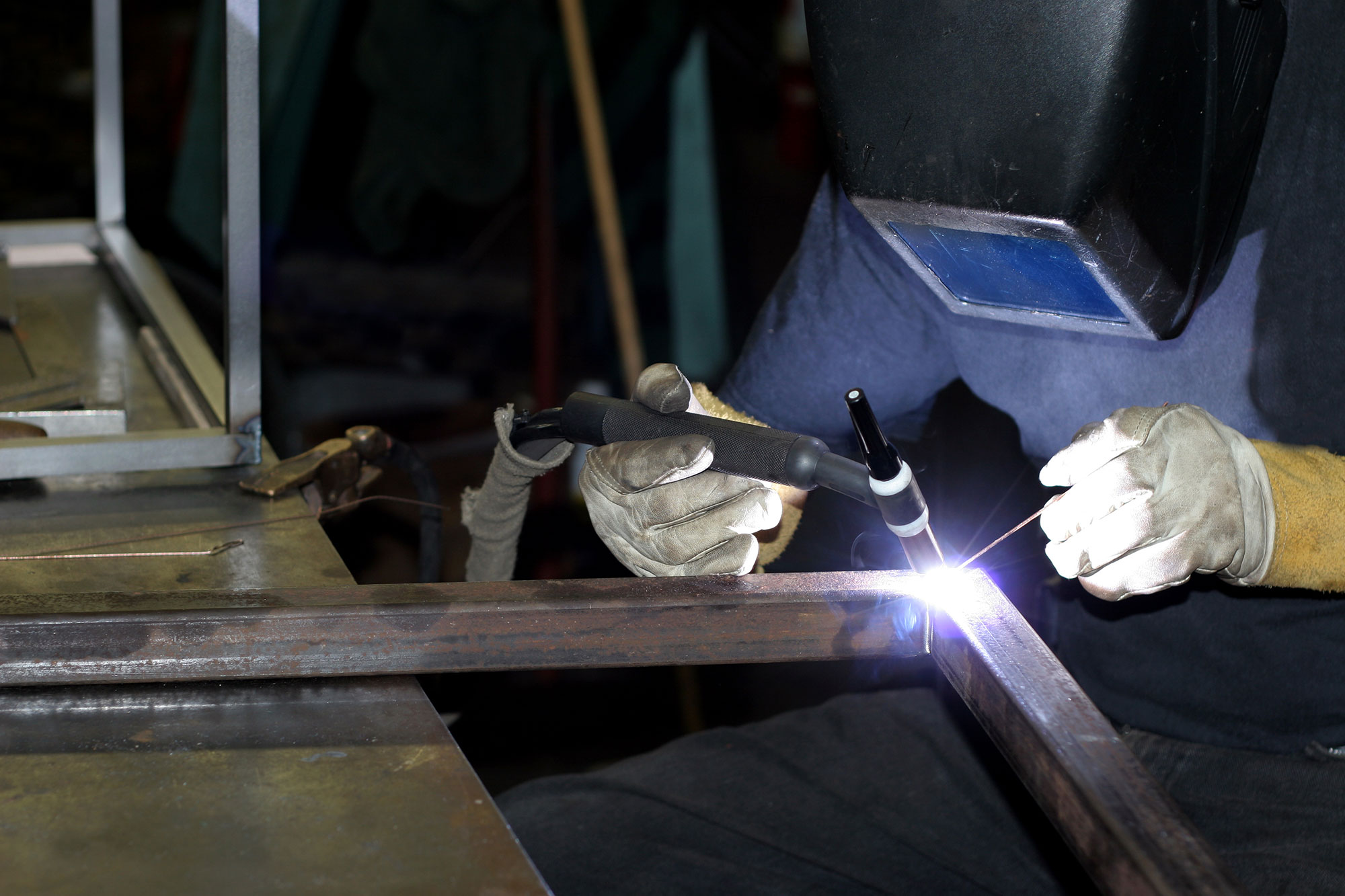
Another arc welding process often used for joining metal components is the TIG (Tungsten Inert Gas) process. While this process makes use of power sources similar to those used for stick welding, TIG also makes use of shielding gas, similar to MIG welding. Pure argon is the most common shielding gas choice for the TIG process and helium is commonly used in cases where additional weld penetration is desired. While MIG welding equipment controls the feed of shielding gas and filler metal into the weld puddle, TIG welding relies on the operator to control the feed of the filler metal (rod, often 1/16” to 1/8” in diameter) into the weld puddle while operating the torch with their other hand, and in many cases using one foot to start/stop the arc and adjust the weld current. The TIG process is similar to gas welding where an Oxygen/Acetylene torch heats the weld area to form a puddle (molten area) with one hand while feeding the filler rod in with the other. However, TIG makes use of an electrical arc traveling between a tungsten electrode and the workpiece to generate the heat required to generate the weld puddle rather than flame or a less constrained arc and as such is able to provide very precise and localized heating of the welded materials. That being the case, TIG produces a smaller HAZ (Heat Affected Zone) relative to that which results from other welding processes, thereby minimizing adverse effects on the welded materials. Another area where the TIG process differs from MIG and stick welding is regarding the control of the arc current. While it is possible to make use of a fixed current to complete a TIG weld, a TIG welder (machine) often makes use of a foot pedal that allows the weldor (person) to ramp the current up and down as necessitated by the needs of the weld joint. Making use of shielding gas and a stable and precise arc, the TIG process produces a clean, spatter, and slag-free weld joint. When performed by a skilled weldor, the TIG process is capable of producing a very aesthetically pleasing weld joint relative to those produced by other processes.
TIG welded joint – steel
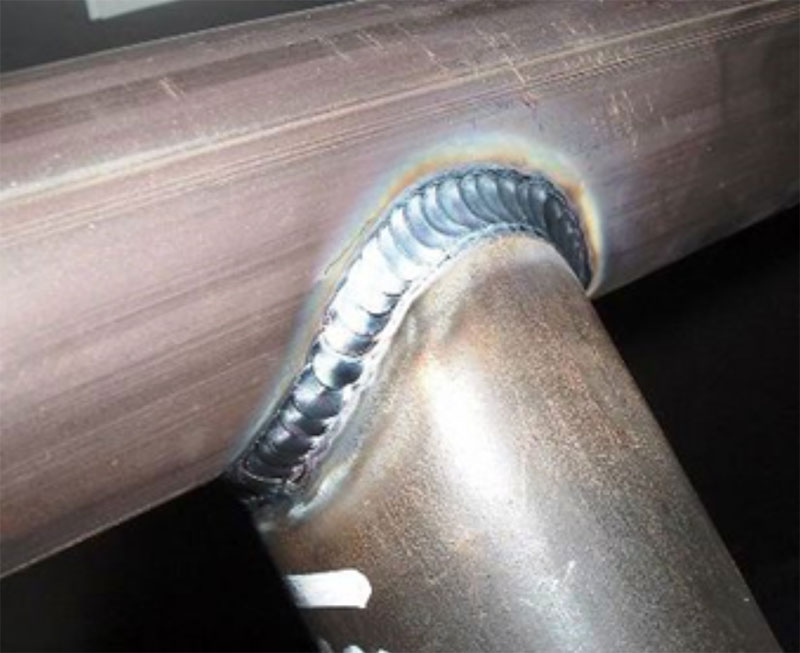
TIG welded joints – aluminum
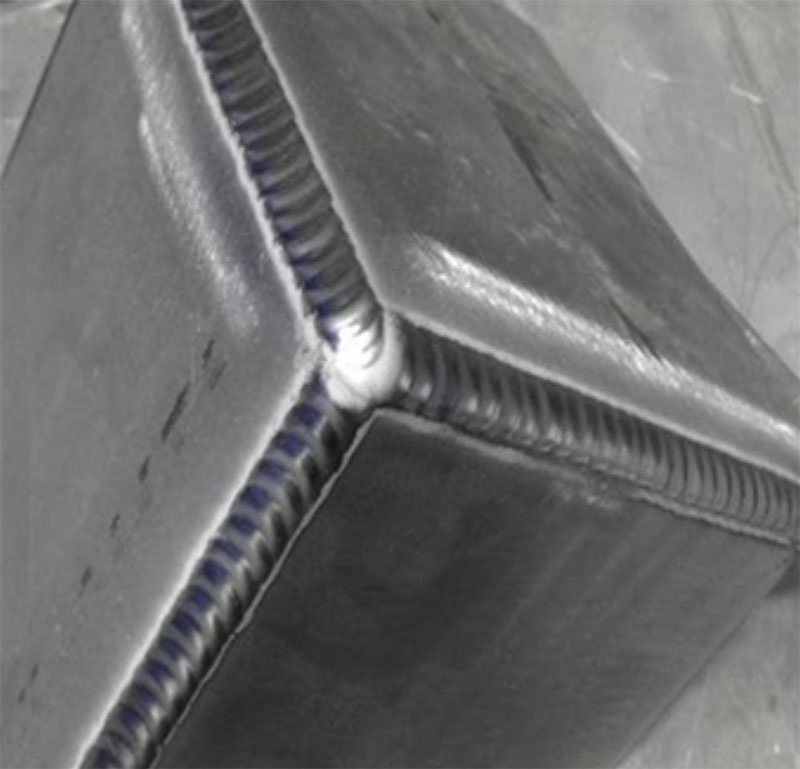
In summary, the TIG process is difficult to master, it requires the use of well-cleaned and tightly fitted materials and it is also much slower than other popular weld processes. As such, using TIG welding to join items is also more expensive to complete than alternative processes – this being the case TIG is reserved for critical applications where other processes are inadequate, or those where the end-user is willing to pay extra for a more visually appealing end product.
While we have discussed a few common arc welding processes here, the universe of welding is vast and comprised of a variety of innovative and fascinating processes for the joining of materials. The processes we discussed here are employed by many and accessible to all, ranging from hobbyists to highly skilled craftsmen. Regardless of the arc welding process chosen for a given application, all of the above discussed are subject to the influence of a large number of variables. As such, weld deficiencies and failures can take many forms -some are readily observed while others are more subtle and require use of more advanced methods. That is something we look forward to discussing at greater length in a future post.
About the Author
Chris S. Spies, P.E. is a consulting engineer with our Kansas City, MO office. Mr. Spies provides consulting services in the areas of vehicle systems analysis, mechanical system and component failure analysis, and industrial/commercial equipment failure analysis. You may contact Chris for your forensic engineering needs at cspies@edtkc.com or (913) 859-9580
Learn about how EDT Forensic Engineering & Consulting approaches cause of damage, and forensic engineering by assigning a file today.