Paper Production
Even in today’s world of electronic communications and the “paperless office”, paper and paper products are a significant material in all of our lives. The value of paper products, such as bathroom tissue and paper towels was evident to anyone looking to find these products during the course of the COVID 19 pandemic. For a material as common in our lives as paper, few people actually know how paper is made; most people just know that paper is made from wood. However, how a hard material such as wood is transformed into a material suitable for cleaning up after using the restroom, is often a mystery. There are a number of processes used to manufacture paper, but this series of blogs will address the most common process used, known as the Kraft Process, which uses caustic (sodium hydroxide, otherwise known as lye) to break down the wood.
From Trees in the Forest to Pulp
Trees are harvested from the forest, then are cut into logs, which are transported by truck, rail or floated down river to the paper mill. Once unloaded at the paper mill, the bark on the logs is removed then the logs are fed into a machine that reduces the logs into small chips. Wood is comprised of cellulose fiber and lignin, of which the cellulose fiber is used to make paper. The lignin can be thought of as a “glue” that binds the fiber in the wood. In order to separate the fiber from the lignin, a process known as digestion is used, whereby the chips are placed inside a large vessel known as a digester. A caustic based liquid, known as white liquor, is pumped into the digester, then the chips are cooked under high pressure and temperature. During the cook process, the white liquor dissolves the lignin, “unlocking” the fiber in the wood. The fiber produced by the digestion process is known as pulp. Photos of chips and pulp are shown below:
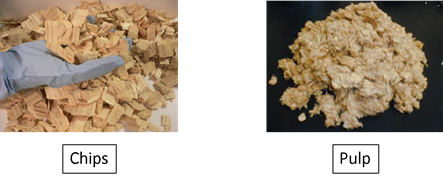
The lignin turns the liquor to a black color, hence liquor leaving the digester is known as black liquor. After completion of cooking, the pulp and black liquor exit the digester, and enter a vessel where the pulp is separated from the black liquor. The pulp is then washed to remove any residual black liquor, then bleached (if white paper is being produced), mixed with water and sent to a paper machine.
Paper Sheet from Pulp
At the paper machine the pulp and water mixture is first laid onto a moving screen, producing a layer of wet pulp. In the initial stages of the paper machine most of the water is removed so as to permit the fibers to form a continuous sheet of paper. The sheet of paper then travels the length of the paper machine passing between steam heated rolls which serve to further dry the paper and to compress the fibers, forming a strong continuous sheet of paper. A photograph showing an example of the drying section in a paper machine is shown below.
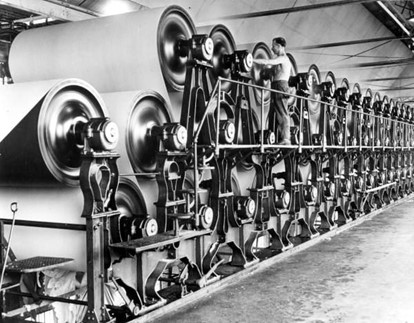
Recovery of the Liquor
The black liquor leaving the digesters is processed in vessels known as evaporators, which “evaporate off” the water in the black liquor, serving to increase the concentration of the organic solids (lignin and other materials removed from the wood) to approximately 60 percent. The high organic solids content of the concentrated black liquor makes the black liquor a useful source of fuel to be burned in a special type of boiler known as a black liquor recovery boiler (BLRB). The BLRB produces high pressure steam for other uses in the mill, including the generation of power in a steam-turbine generator.
In addition to the organic solids, the black liquor also contains sodium, the main ingredient in the white liquor. Inside the BLRB, the organic material is burned, while the sodium compounds are left behind, forming a molten, glass-like material known as smelt, which is collected at the bottom of the BLRB. The smelt flowing from the BLRB is cooled and dissolved in water, where the mixture then is known as green liquor. The green liquor is further processed by the addition of lime, with the resulting liquid becoming the white liquor to be reused in the digester. The liquor “circle of life” for a typical Kraft pulp mill is shown below:
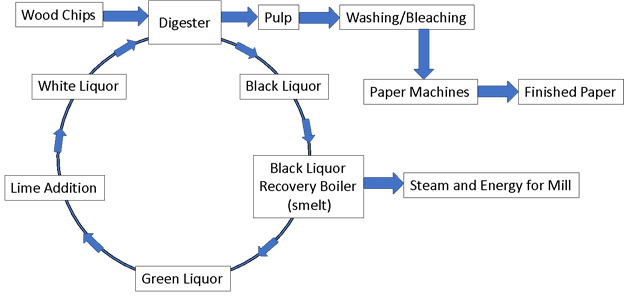
In the next few blogs surrounding Paper Production, we will be discussing corrosion and damage issues associated with the Kraft process.
About the Author
Thomas D. Traubert, P.E. is EDT's Chief Engineer and consulting engineer with our Hartford, CT office. Mr. Traubert's assignments are primarily associated assignments in the chemical, refining, pulp and paper, power and steel industries. You may contact Tom for your forensic engineering needs at tdtraubert@edtengineers.com or (860) 285-8000.
Learn about how EDT Forensic Engineering & Consulting approaches cause of damage, and forensic engineering by assigning a file today.