Dezinci – What??? What Is Dezincification?
As a result of changes in the regulations and restrictions for potable water systems by the NSF Standard 61: Drinking Water System Components Health Effects, the use of lead in brass alloy fittings, faucets, and components was eliminated. It should be noted that lead was used in brass alloys to decrease the costs associated with the machining process (i.e., cutting, milling, etc.) during manufacturing. It should also be noted that lead was replaced by zinc. However, during the introduction of zinc into brass alloys, a new challenge, dezincification, was identified.
The ASM Handbook, Volume 2, Failure Analysis and Prevention, defines dezincification as “Corrosion in which zinc is selectively leached from zinc-containing alloys. Most commonly found in copper-zinc alloys containing less than 85% Cu after extended service in water containing dissolved oxygen.” The ASM Handbook also defines selective leaching as “Corrosion in which one element is preferentially removed from an alloy, leaving a residue (often porous) of the elements that are more resistant to the particular environment.”
The ASM Handbook, Volume 13, Corrosion, Dealloying states, “Dealloying is a corrosion process in which the more active metal is selectively removed from an alloy, leaving behind a weak deposit of the more noble metal. Copper-zinc alloys containing more that 15% Zn are susceptible to a dealloying process called dezincification. In the dezincification of brass, selective removal of zinc leaves a relatively porous and weak layer of copper and copper oxide. Corrosion of a similar nature continues beneath the primary corrosion layer, resulting in gradual replacement of sound brass by weak, porous copper. Unless arrested, dealloying eventually penetrates the metal, weakening it structurally and allowing liquids or gases to leak through the porous mass in the remaining structure.”
With the use of EDT’s Kansas City District Office Scanning Electron Microscope (SEM) and Energy Dispersive Spectroscopy (EDS) which uses X-Ray technology to determine material composition (i.e., atomic elements), a brass push-to-connect fitting was examined that exhibited dezincification. A detached section of the fitting was placed into the SEM/EDS and four locations were examined and documented. The SEM/EDS revealed the detached section exhibited four locations with a cast brass alloy material composition consisting of:
1. 58.39% copper (Cu) and 38.70% zinc (Zn)
2. 57.15% copper (Cu) and 38.00% zinc (Zn)
3. 44.02% copper (Cu) and 32.92% zinc (Zn)
4. 25.86% copper (Cu) and 36.47% zinc (Zn)
As such, the detached section of the copper-zinc alloy fitting exhibited copper (Cu) measurements that were less than 85% (Cu) and zinc (Zn) measurements that were greater than 15% zinc (Zn). The measured zinc (Zn) ranged from 32.92% to 38.70% of zinc (Zn). Therefore, the copper-zinc alloy exhibited zinc measurements greater than 15% Zn, selective leaching of zinc, and dealloying process indicative of dezincification.
Below are screenshots of the Scanning Electron Microscope (SEM) and Energy Dispersive Spectroscopy (EDS)
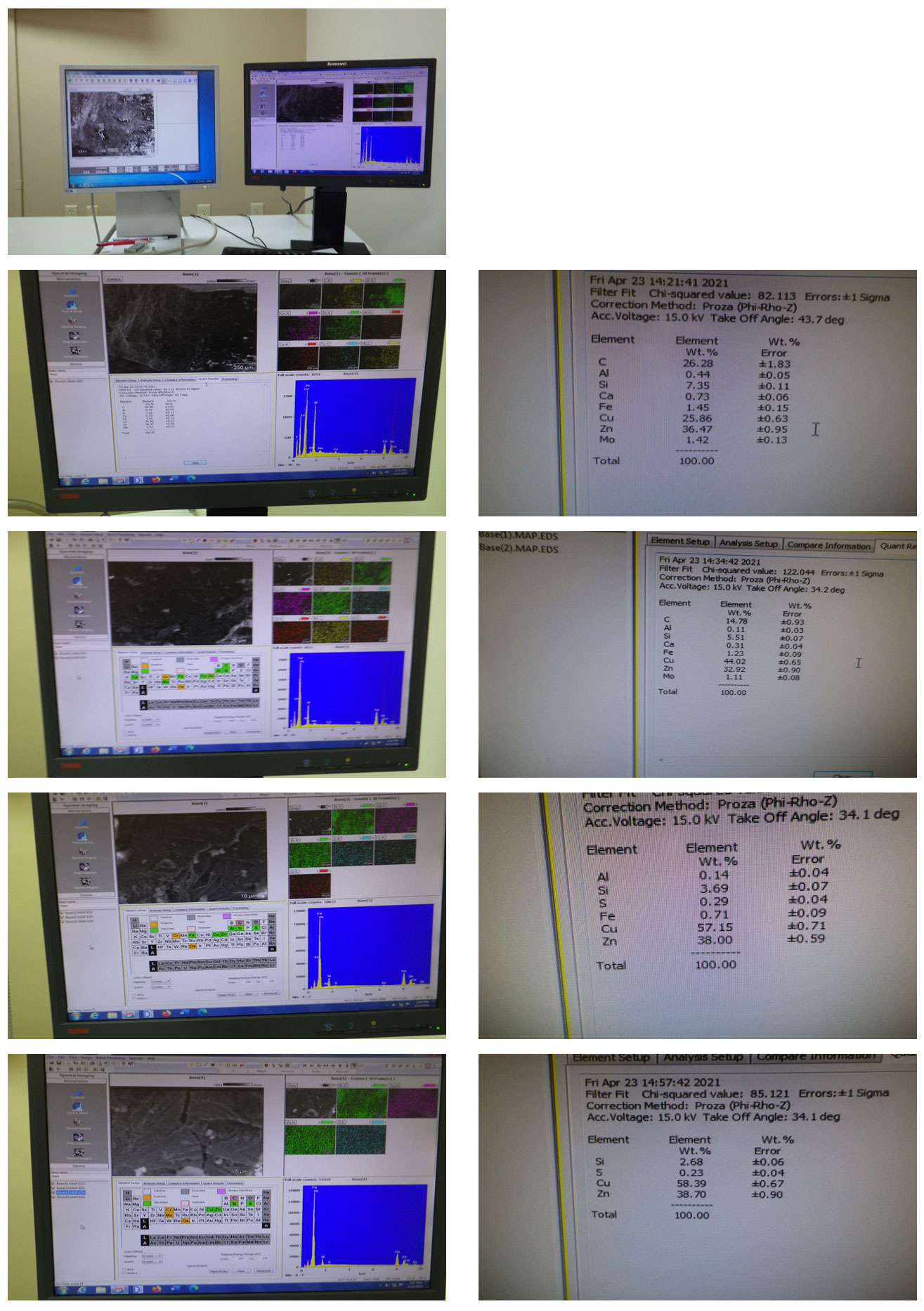
About the Author
Richard L. Ellsworth, P.E. is a consulting engineer with our Kansas City Office. Mr. Ellsworth provides consulting services in the investigation and analysis of mechanical fractures/failures of materials and components, mechanical systems, and equipment specifications. You may contact Rick for your forensic engineering needs at rellsworth@edtkc.com or (913) 859-9580.
Learn about how EDT Forensic Engineering & Consulting approaches investigation and analysis of mechanical fractures/failures of materials and forensic engineering by assigning a file today.